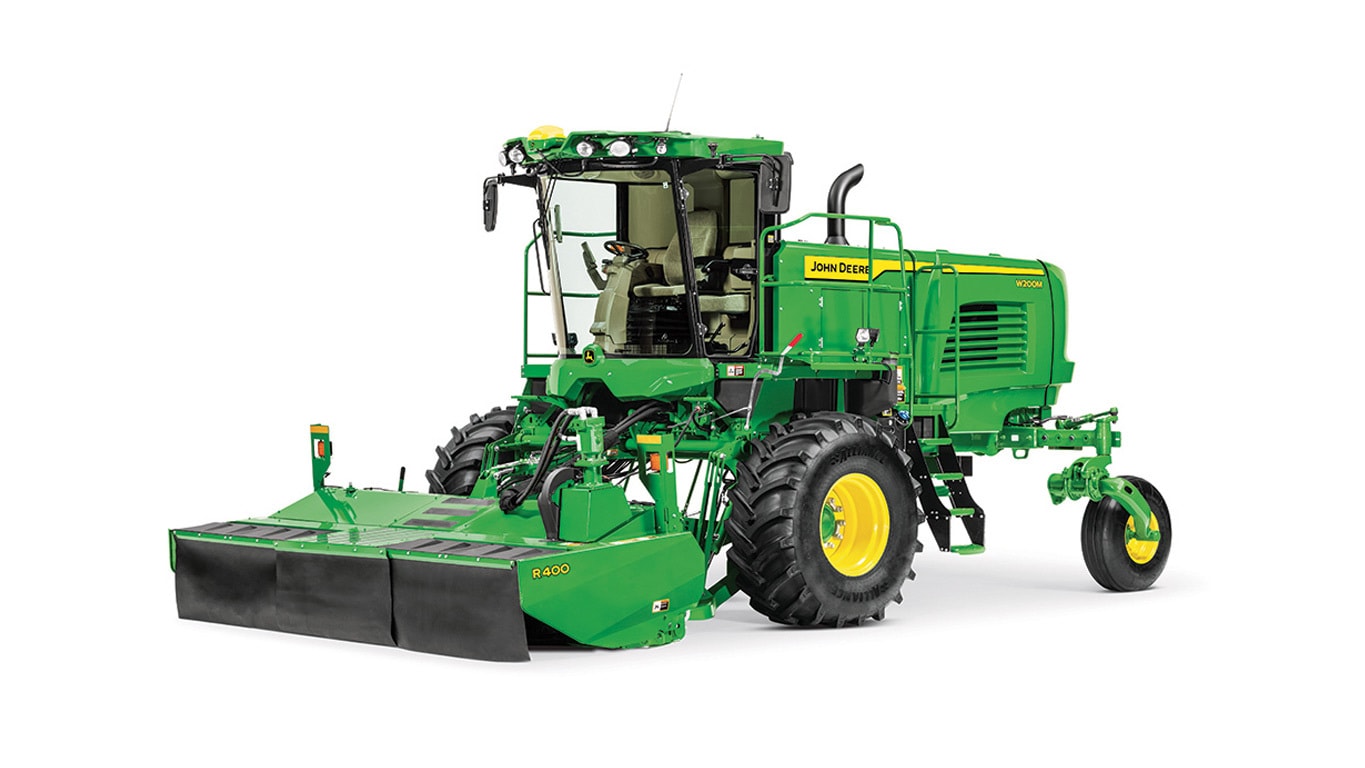
R400 Rotary Platform
- John Deere
- Windrowers
Find Your Nearest Location
Key Features & Specs
- 13 ft. (4 m) cut width
- Compatible with W200M and W235M
- Impeller, Urethane or V10 conditioning options
- Quick Change Knives
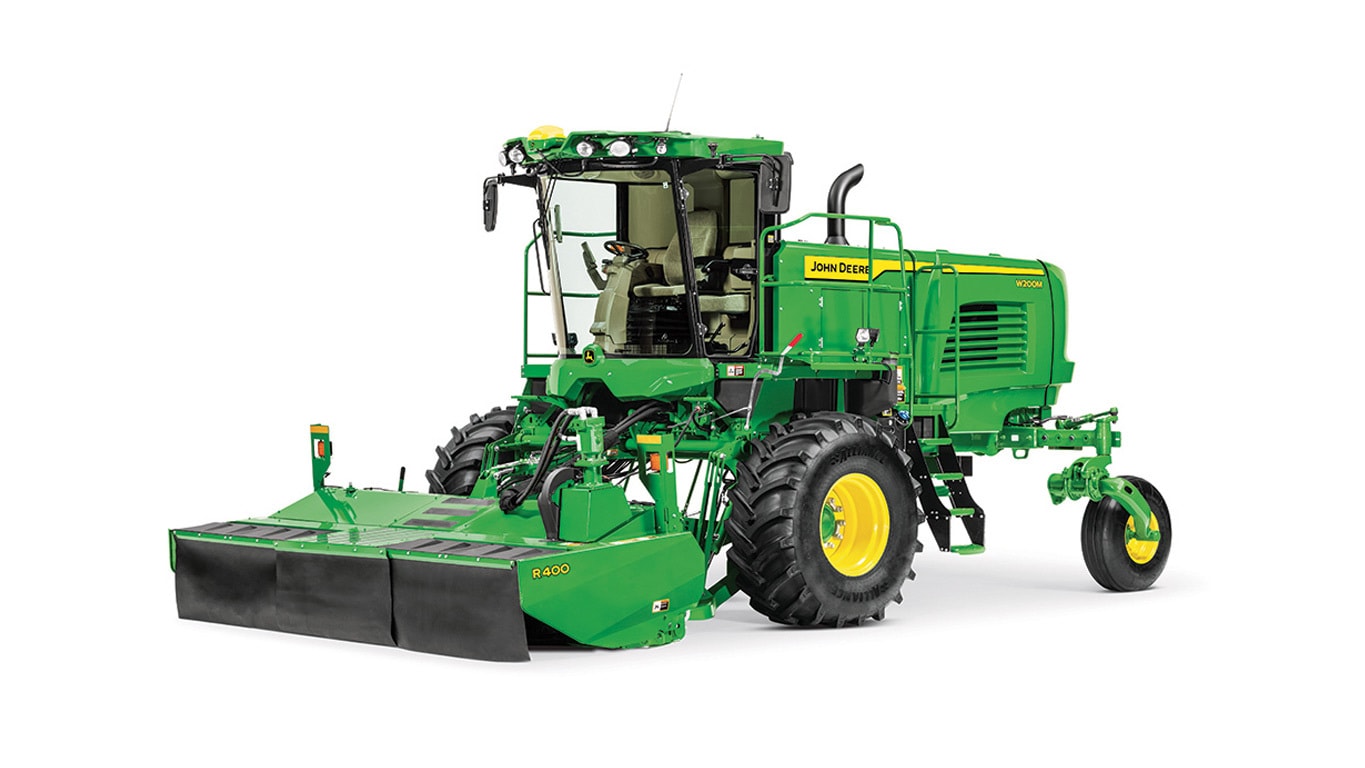
- + Expand All
- - Close All
-
Improved performance and durability from rotary cutterbar components
- Large oval disks with free-swinging knives
- Designed to retract when striking solid objects
- Wear caps, crop accelerators, and strippers deliver improved platform performance and lowered cost of operation
Knives and disks
Oval disks with free-swinging knives
- Reversible knives double the useful life
- Located at the front of the cutterbar for ease of serviceability
- Knives are identical, making servicing simple
- Disks are made from high strength austempered steel, a heat-treating process that ensures the steel is thoroughly and evenly tempered for good wear characteristics
- Cutting disks rotate toward the center of the platform except for disks 3 and 8, which rotate away from center. The paired rotation of disks 3 and 8 feed crop into the cross auger and help form more uniform edges of the windrow.
Wear caps
Wear caps
- Wear caps are installed on each end of the cutting disks (except on the end disks where crop accelerators are used) to increase the wear life of the cutting disks and knife bolt nuts.
- Wear caps are open on the end to prevent debris from packing in close to the nut, making hardware and knives easier to change.
Crop accelerators
Crop accelerator
- Crop accelerators are added to disks 1, 4, 7, and 10. Accelerators on disks 4 and 7 help to move crop from the diverging area between disks 3-4 and 7-8 and into the conditioning rolls.
- Wear can be determined when a hole becomes visible in the end or the top of the accelerator and replacement is needed (performance may deteriorate before a hole is visible).
- The one-piece design includes a heat-treated steel wear cap that protects the knife bolt nut and the end of the cutting disk.
Rotary strippers
Rotary stripper
- Rotary strippers are bolted to the bottom of the inner converging drum on both the left side and right side of the platform.
- Rotary strippers improve crop flow and convergence to the conditioner and minimize crop recirculation, improving windrow formation and crop quality.
- Relocating the stripper to the converging drum provides increased wear life of the converging drum and less buildup of dirt and mud on the cutterbar, delivering lower cost of operation and increased uptime.
- Rotary strippers are made from high-strength, austempered steel for improved wear life.
-
Quickly adjust rotary header settings with TouchSet™ technology
Adjustment to the rotary header can be made from the cab if TouchSet is ordered on the R500. You can adjust the formation shields and swath flap on the go.
Windrow width adjustments
To perform windrow width adjustments previously, you had to crawl under the machine to loosen and adjust the forming shields.
Adjust the swath flap from the display
Adjust the forming shield from the display
With TouchSet, the operator can select and adjust the swath flap and forming shield settings easily right from the display.
TouchSet is not compatible with the R400. It is compatible with the R500 equipped with any conditioner except for the impeller.
Windrow formation shield actuators
Customize a preset for a field or crop
TouchSet comes with a preset library of different crops to select while cutting. The crop selection automatically adjusts the header for that particular crop. You can also customize your own preset for a particular field and/or cutting. This allows you to quickly adjust the swath flap, forming shields, head tilt, and cutterbar speed.
-
Quick and easy serviceability with lightweight doors and replaceable top sheets
Lightweight plastic doors and bolted top sheets make service quick and easy.
Lightweight plastic doors
- Lightweight plastic doors provide resistance to rock damage and are easier to open than original metal doors.
- Bolted top sheets replace an original welded design and can be removed for increased accessibility or replaced in case of rock damage.
-
Save time with quick-change knives
Quick-change knives
Having sharp knives on your machine is critical to harvesting all your crop and leaving a clean-cut field. Changing dull or bent knives is no longer a time-consuming job with the John Deere quick-change knife (QCK) system. There are no worries about having an impact or air compressor to change out the bolts. Simply insert the QCK tool into the disk and press down. The knives can be swapped out in seconds.
- Reduce time to change knives by more than 50 percent over the bolted system
- Base equipment for every John Deere mower conditioner
- Kits are available to retrofit most 600, 800, and 900 Series Mower-Conditioners
-
Even crop flow from the edges with the overshot cross auger
The overshot cross auger delivers increased performance in windrow formation and cut quality. Improved crop flow from the edges of the platform toward the center provides an even flow into the conditioner, creating more uniform windrows. Additionally, crop is lifted off the cutterbar faster for improved cut quality in downed crops and reduced crop recut.
Improved crop flow from edges
- The overshot cross auger features cupped flighting with a long pitch. The cupped shape makes the auger more aggressive in pulling crop from the edges of the platform and the converging drums.
- Moving more crop from the edges of the platform toward the center delivers increased windrow uniformity, helping to reduce drydown time.
Reduced recut
Reduced recut
- The center flutes of the cross auger have an aggressive edge to help lift crop off the cutterbar and feed it faster into the conditioner. This improves crop quality in reducing the potential for crop recut.
- Moving crop faster into the conditioning rolls increases the overall capacity of the platform, enabling faster cutting speeds in heavier crop and more acres cut in a day.
-
Maximize performance in varying crops with a choice of conditioners
The R400 and R500 Rotary Platforms offer choices of conditioners to meet producer needs. Varying crop types require different conditioners to deliver maximum performance in terms of window formation, cut quality, and drydown time.
Urethane conditioning rolls
Urethane conditioning rolls
- The urethane roll conditioner works well in legumes, especially alfalfa and most all-grass crops. In general, roll conditioners are better suited for thick- stemmed, cane-type, and taller grasses more than 1.5-m (5-ft) tall.
- Molded urethane rolls are formed by a cool molding process that does not distort or warp the steel core of the roll, ensuring the rolls are arrow straight and cylindrical, so they can be accurately spaced close together for uniform conditioning along the length of the roll.
- The intermittent, recessed-cleat design gives more crimping edges for greater pressure per square inch, which results in superior conditioning and faster crop drying.
An adjustable swath board is included with the urethane conditioner roll option.
Impeller
Free-swinging impeller
Pre-loaded tine impeller
The free-swinging impeller is available only on the R400 Rotary Platform. The pre-loaded tine impeller is only available on the R500 Rotary Platform.
The impeller conditioner works well in grass crops and legumes such as alfalfa. The V-shaped impeller tines produce a scuffing action by pushing crop against the adjustable conditioning hood, which helps remove the waxy surface of the stem to allow for faster evaporation of moisture. It is not recommended to use this conditioner with crops that are 1.5 m (5 ft) or taller.
The adjustable conditioner hood allows the operator to increase or decrease the distance between the hood and impeller tines. A tighter clearance provides more aggressive conditioning, while a wider setting allows for a higher volume of crop or less aggressive conditioning for use in legumes. The impeller rotor speed can also be adjusted by changing drive belt routing.
The R400 has free-swinging impeller tines to help prevent damage to the conditioner if rocks or other solid objects are struck, reducing maintenance in adverse conditions. The R500 has a pre-loaded tine impeller with 162 tines. Tines are individually replaceable as needed for wear or breakage. Machines should never be operated with missing or broken tines, as it can cause an imbalance and vibration leading to damage.
Impeller speeds:
- 870 rpm – ideal for grasses
- 630 rpm – suggested setting for legume crops
- Increased impeller speed in taller crops may help reduce wrapping of rolls
V-10 steel conditioning rolls
Close-up of V-10 steel conditioning rolls
- The V-10 steel conditioner rolls feature 10 angled flutes arranged in a chevron pattern, or V-pattern, along the length of the steel core.
- Steel rolls offer improved wear life over urethane rolls, particularly in adverse crop conditions.
Advantages of the V-10 conditioner roll over the previous straight-flute design include:
- Deep intermeshing angles for positive feeding and uniform conditioning throughout the entire length of the rolls
- More crimping edges for improved conditioning
- Improved feeding
- Improved windrow formation
An adjustable swath board is included with the V-10 steel conditioner roll option.
Tri-Lobe™ steel conditioning rolls
Tri-Lobe steel conditioning rolls
Close-up of Tri-Lobe steel conditioning rolls
- Tri-Lobe steel conditioning rolls have three intermeshing chevron lobes to crush the length of the stem for improved conditioning and faster drydown. The rolls are manufactured using a patented process.
- The steel material increases wear life, especially in abrasive crops or soil conditions. Durability is a distinct advantage compared to other crusher-style rolls made of rubber or urethane. The chevron design of the rolls gives positive feeding and improved crop flow.
- These rolls are well-suited for use in alfalfa where reduced curing time results in less bleaching of the crop. In heavy, thick-stemmed crops, such as sudan or sudex, the steel construction of the rolls does a very good job of breaking up the nodes on the stems to improve dry down.
Replaceable end shafts
- The shafts on the Tri-Lobe rolls are steel forgings that are then machined. These precision parts have minimal runout, which means the rolls themselves rotate precisely around their axis.
- This precision enables the rolls to be adjusted to a minimum clearance for consistent conditioning along the length of the rolls.
- The machined, forged roll ends are bolted into the core of the Tri-Lobe steel roll. In the event a roll end is damaged, the entire roll does not need to be replaced. Each shaft can be replaced individually, resulting in lower repair costs.
- For serviceability, each roll end has two threaded holes so bolts can be used to pull the shafts from the steel core of the roll.
An adjustable swath board is included with Tri-Lobe conditioner option.
-
Uniform windrow formation provided by frame, swathboard, and forming shields
The R400 and R500 Platforms deliver the latest advancements in windrow formation and uniformity from John Deere. Even, uniform windrows are critical to reducing drydown times for dry hay and providing consistent chopping speeds and cut lengths for forage harvesting applications.
Angled frame
Angled frame
- The R400 and R500 features an angled frame to help merge the crop into the forming shields.
- Merging crop directly behind the conditioning rolls provides a smoother transition to the forming shield, creating a more uniform windrow.
Swathboard
Swathboard
- The swathboard is critical to windrow formation as it controls the angle at which the crop contacts the forming shields.
- The welded pipe connecting the adjustment arm to the swathboard provides rigidity, preventing the swath board from bouncing and causing bunching in the windrow.
Forming shield
Forming shield adjustment
Forming shield attachment
- Forming shields are easily adjusted to control the material flow, allowing the operator to match the windrow width to the harvesting requirements.
- The windrow width is adjustable, without the use of tools, from a narrow windrow to a wide, fast-drying swath:
- 4 cm (36 in.) up to 216 cm (85 in.)
- NOTE: The windrow width depends on the crop conditions and type of conditioner.
- Attaching the forming shields to the platform is simple. The shields hang on a cantilevered bolt with spacer and are held in place with a single bolt.
Fixed fluff board
Fixed fluff board
- The fluff board at the rear of the forming shields is fixed in the ideal position to deliver optimal performance in all crop conditions.
-
Easily change out and service the modular-designed cutterbar
The John Deere-patented-design cutterbar is made from individual, diagonal-cut modules. Servicing the modules is easy; the diagonally-cut module design allows the modules to be removed individually while leaving the cutterbar attached to the frame. Idler gears transmit power through the cutterbar, increasing life of the platform and improving uptime.
Diagonal-cut modules
Cutterbar module
- Removing seven bolts (two on each side of the module and three at the rear of the frame) enables a module to be removed from the cutterbar.
- A rubber ring seals each module to the other and enables a common oil reservoir throughout the cutterbar.
- The modules are made of high-strength, nodular iron castings.
Drive components
Cutterbar drive components
- Each module consists of two idler gears and one drive gear. The large-diameter idler gears transmit power from module to module. The idler gears turn at a relatively slow speed for added durability.
- A smaller-diameter pinion drive gear is used only to power the cutting disk. Power is not transmitted from one cutting disk to another except through the large- diameter idler gears.
- Cutterbar modules are interchangeable across the entire cutterbar. Disk rotation is reversible and determined by the quill position (A) when assembling the disk module to the cutterbar. In some conditions, cutting performance can be improved through reversing individual disk rotation.
Dimensions
Cutting width | 5 m 16 ft |
Weight | With impeller conditioner 2,135 kg 4,707 lb With fluted steel conditioner 2,371 kg 5,229 lb With urethane conditioner 2,263 kg 4,990 lb With Tri-Lobe conditioner 2,426 kg 5,350 lb |
Overall width (transport) | 5 m 16.3 ft |
Cutting height | 1.7-17.8 cm 0.7-7 in. |
Windrower width (depending on crop conditions) | With roll conditioner 91-216 cm 36-85 in. With impeller conditioner 114-216 cm 45-85 in. |
Impeller conditioner
No. of V-tines | 72 |
Conditioner hood | Adjustable, one lever |
Drive | 4-V powerband belt and sheaves |
No. of speeds | Two-factory setting 624 or 865 rpm Optional 1,000 rpm |
Width | 2.7 m 8.8 ft |
Diameter | 59.4 cm 23.4 in. |
Key Specs
Compatibility | 4995, R450, W235, W260 |
Cutting width | 5 m 16 ft |
Overall width (transport) | 5 m 16.3 ft |
Cutting height | 1.7-17.8 cm 0.7-7 in. |
Weight | With fluted steel conditioner 2,371 kg 5,229 lb With urethane conditioner 2,263 kg 4,990 lb With Tri-Lobe conditioner 2,426 kg 5,350 lb |
Rotary disk cutterbar
Guard angle | Adjustable; 0-8 degree (angle) |
Number of disks | 10 |
Reservoir capacity | 9.5 L 12 U.S. qt |
Steel conditioner rolls
Drive | Enclosed gear and shaft drive |
Surface | Intermeshing flutes |
Speed | Platform speed 865 at 2,650 rpm |
Material | Steel |
Width | 2.7 m 8.8 ft |
Diameter | 25.4 cm 10 in. |
Urethane conditioner rolls
Surface | Intermeshing, intermittent recessed cleats |
Speed | Platform speed 865 at 2,650 rpm |
Material | Urethane |
Drive | Enclosed gear and shaft drive |
Diameter | 25.4 cm 10 in. |
Width | 2.7 m 8.8 ft |
Windrower
Compatibility | 4995, R450, W235, W260 |
Formation | Adjustable fluffboard and adjustable forming shields |
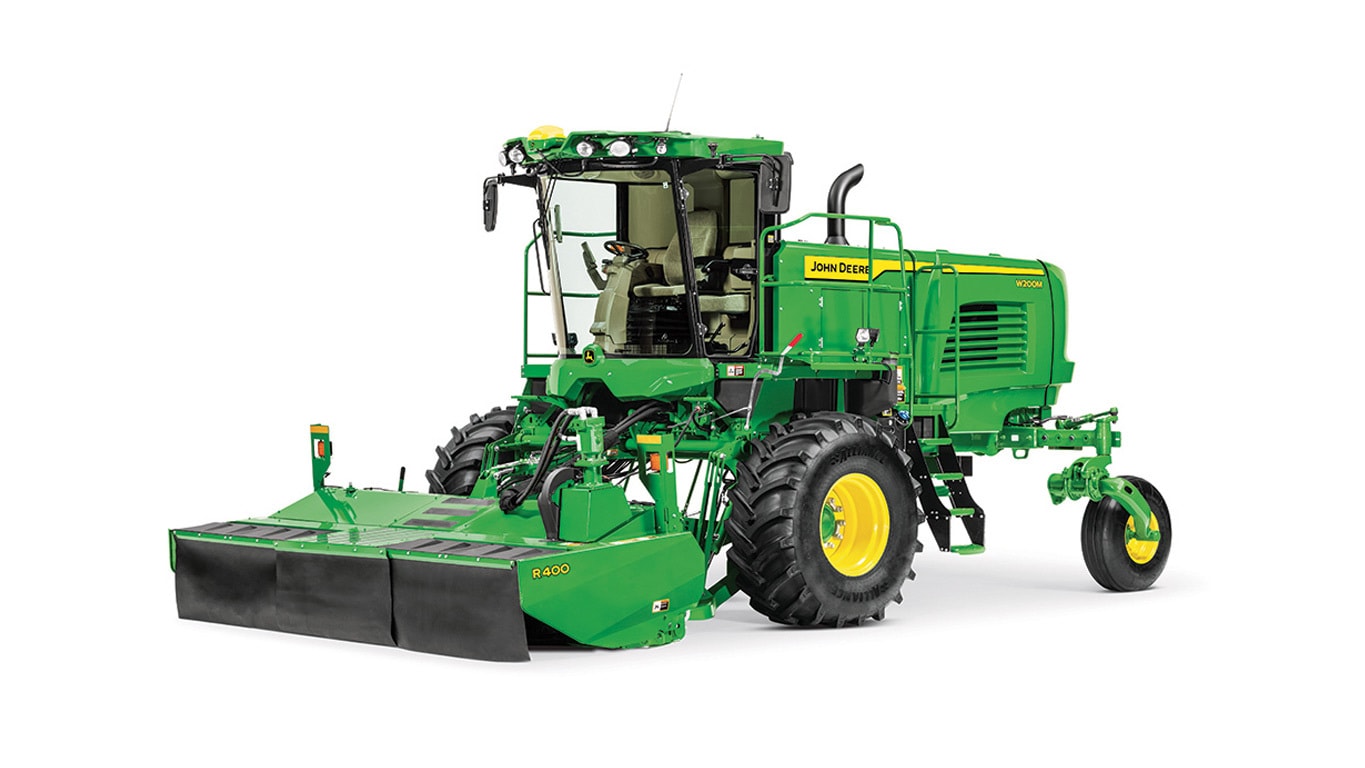